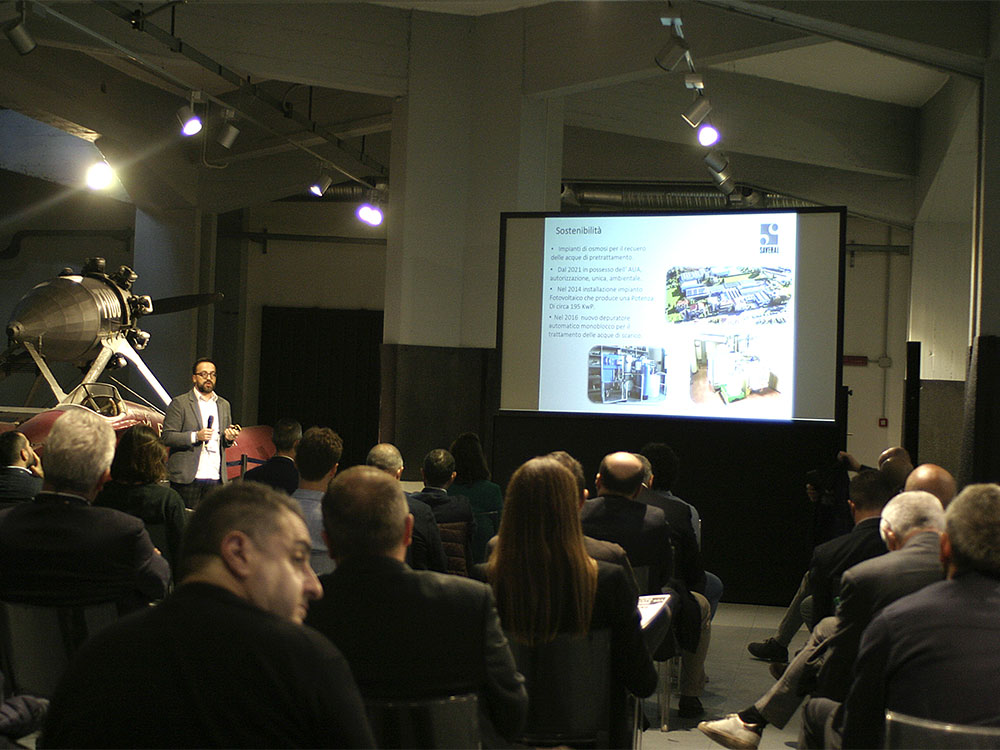
Saveral, from precursor of powder coating to innovator
Founded in 1954 by Abele Preda, Saveral began as a small tank phosphating plant in Almenno San Bartolomeo, in the province of Bergamo, specialising in galvanic processing on behalf of third parties. Over the years, the company has become a reference point in numerous sectors, equipping itself with three powder coating plants to meet the needs of diversified sectors.
Saveral has established itself as a reliable partner for some leading Italian and global industrial companies, including Brembo, Tino Sana, Rancilio, La Cimbali and Toora. ISO 9001, 14001 and 45001 certified the company as committed to guaranteeing high-quality standards, constantly demonstrating the will to improve, and offering excellent service.
P&E Coating Days in Milan
During the P&E Coating Days in Milan last October, the Akzo Nobel Powder Coatings testimonials (including Saveral) were awarded the TOP Award, a recognition given to companies that adopt environmentally sustainable painting products and technologies while maintaining high-quality standards for “busbars,” i.e., copper, brass, or aluminium bars used for the distribution of electricity within an electrical panel.
To date, the painting systems are constantly updated with the most high-performance technologies. Wagner supplies the new generation powder coating booths and related equipment. They are equipped with automatic application systems, which are essential to obtaining uniform and replicable results requested by customers. However, manual retouching stations are available before and after automatic painting when necessary.
Saveral and the Innovation Process
Our innovative approach is always in progress. In 2022, we integrated state-of-the-art machinery that allows us to optimise processes and improve the quality of our products: the IPS System. This powder dosing and application system offers several advantages, including:
- Exact dosing of the powder, which permits the optimisation of thicknesses in productions with pieces that have remarkably differentiated geometry and morphology, leading to the saving of powder.
- Consistent delivery over time, guaranteeing a high-quality standard and reducing waste.
- Easy management of application parameters, simplifying and making it intuitive to adjust the parameters.
- Greater penetration in the undercuts, reducing consumption and the need for manual retouching.
- Delivery efficiency, thanks to the optimal balance of the kinetics of the powder in delivery and the electrostatic parameters, reducing manual touch-ups and thus eliminating interruptions on the most complex pieces.
- Repeatability of results over time, thanks to the consistency of the application parameters, ensuring the consistency of the quality standards and eliminating the need for dispenser adjustments.
In 2023, we optimised an existing plant by moving it and installing a new paint booth. In 2024, we will continue with another optimisation of an existing plant and purchase a pre-treatment-related drying plant.
Through these investments, we intend to meet our customers’ needs through innovative and sustainable solutions. Contact us!